倉庫で行われる色々な作業の中で特に割合が大きいのがピッキングです。
そのため、ピッキングを効率的に行い、早く済ませることができるようになれば倉庫全体の生産性も高まります。
ただし、作業員にただ早く動くように求めても、ミスが発生したり、事故が発生したりする原因になってしまいます。
これでは対処に追われて逆に作業が長引いてしまうでしょう。
ピッキングを効率的に行うためには倉庫内の環境などピッキングに関わるあらゆる部分を見直し、スムーズに作業ができるように改善することが求められます。
そこで、今回はピッキングを効率化するためのポイントをご紹介していきます。
倉庫の生産性を上げたい、いつも時間内に作業が終わらなくて困っているという方はぜひ参考にしてくださいね。
倉庫のピッキング作業の効率が悪くなる原因4つ
効率化を進めるためには現時点で倉庫にどのような課題があるのかを把握することが大切です。
課題を知った上で対策をすれば成果も出やすくなります。
これからピッキングの効率が悪くなるよくある原因をご紹介するので、倉庫にどんな問題があるか考えてみましょう。
商品の場所を見つけるのに時間がかかる
ピッキングはリストに書かれている商品を集めていく作業です。
倉庫内には色々な商品があり、規模が大きい倉庫ではスペースが広いため、商品を探すのに一苦労してしまいます。
何年も勤めている人なら商品名を見ただけで場所が分かるかもしれませんが、新人は慣れていないので特に時間がかかりがちです。
移動に時間がかかる
ピッキングでは倉庫内をひたすら歩き回ります。
環境によっては商品を集めている時間よりも、移動の時間の方が長くなるでしょう。
もし、倉庫のレイアウトが悪く、無駄な移動が多くなってしまう状態だとピッキングにかかる時間は長くなってしまいます。
商品を取り出すのに時間がかかる
商品が箱の中に入れられて棚の中に収められている場合、取り出すのに時間がかかってしまうという課題があるかもしれません。
例えば、箱が大きすぎて手前に引くと棚のフレーム部分に引っかかり、なかなか商品が取れないという事態が考えられます。
些細なことですが、ピッキング中に何度も行われる作業なので、全体で見るとかなりの時間のロスになっています。
また、従業員のストレスを招くというデメリットもあります。
商品を間違えている
ピッキングをしたものの集める商品が違っていたら、正しい物を取りに行き、間違えて集めたものは元の場所に戻さなければならず、対処に時間がかかってしまいます。
人の手によって行われるものなので、ミスはしょうがないことですが、できるだけ減らすための対策が必要です。
倉庫のピッキング2つの種類
ピッキングには2つの種類があり、状況に応じて正しい方を選ぶことで作業時間の短縮に繋がります。
それぞれの特徴をご紹介していきます。
シングルピッキング
受注ごとにリストを出してピッキングする方法です。
商品の種類が多く、少量ずつしか出ない場合や出荷先が多い場合に便利です。
摘み取り方式とも呼ばれます。
トータルピッキング
種まき方式とも呼ばれるトータルピッキングは必要な商品を一度まとめて集めてから、出荷先ごとに仕分ける方法です。
出荷先の数が少なく、扱っている商品が少ない場合にぴったりです。
シングルピッキングに比べると商品を集めるのにかかる時間は少なくなりますが、集めたあとも仕分け作業をしなければならず、工程が1つ増えます。
トータルピッキングでは集めた商品を置く大きいスペースが必要です。
倉庫のピッキング作業を効率化させるポイント10つ
ピッキングを効率化するためには改善できるポイントがいくつもあります。
これからご紹介していくので、取り入れられそうなものから取り入れてくださいね。
移動時間が最小になるようなレイアウトを作る
倉庫のレイアウトはピッキングにかかる時間を大きく左右します。
効率的に移動するためには出荷される頻度が高いものを手前に置き、低いものを奥に配置するのがポイントです。
倉庫の生産性を上げるレイアウトの作り方はこちらの記事でまとめているのでぜひ参考にしてくださいね。
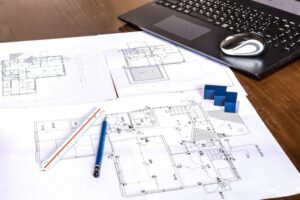
スムーズに取り出せる箱を設置する
商品を箱に入れて管理する場合、一度手前に引くだけでスムーズに取り出せるような箱を用意しましょう。
商品の数だけ箱を用意するのはコストがかかりますが、削減できる時間はとても大きいですよ。
倉庫内の5Sを徹底させる
5Sとは整理、整頓、清掃、清潔、躾の5つで、これらに取り組むことで工場や倉庫の作業環境を整えることができます。
倉庫の場合、整理や整頓ができていなければ商品が違う場所に保管されて作業ミスの原因になってしまうかもしれません。
また、清潔や清掃ができていなければ、倉庫内を移動しにくく、ピッキングに時間がかかってしまうでしょう。
5Sに取り組んでいない場合はこの機会に導入を検討してみてはいかがでしょうか?
倉庫管理システムを導入する
倉庫管理システムは入出庫管理や在庫管理をデジタル化し、倉庫内の物流を管理するシステムのことです。
在庫の状況が瞬時に反映されるため、商品の数が少なくなったときにすぐに補充ができ、在庫がなくなるのを防ぐことができます。
また、ピッキングリストの出力も可能になります。
そのほかにも倉庫管理システムには便利な面がたくさんありますよ。
ハンディを使って作業する
マテハン機器を使ってピッキングをシステム化するのも効率化の方法の1つです。
リストを表示させるタブレット、ハンディ、商品のバーコードをそれぞれ連携させると、違う商品をピッキングしそうになってもブザーを鳴らして警告してくれるので、ミスが発生するのを防ぐことができます。
品出し方法を工夫する
品出しのやり方もピッキングをスムーズにできるかどうかに関わります。
後から商品を取り出しやすいように品出しをすることでピッキングの効率を上げることができます。
品出しをする人の負担は増えますが、ピッキングには何人もの人が関わり、大きな時間を節約することができるので、商品ごとに取り出しやすい品出しの仕方を見つけて、それを浸透させましょう。
作業方法を統一する
ピッキングのやり方が人によって違っていると早くできる人が居る一方で、時間がかかる人も出てきてしまいます。
作業時間を短縮するためには効率的なピッキング方法を確立し、それを全員に取り入れてもらいましょう。
また、マニュアルを作っておけば、新しく入ってきた人も作業方法をすぐに覚えられます。

理解しやすいピッキングリストを作る
ピッキングリストに色々な情報が詰め込まれていると、本当に必要な情報を見つけるのに時間がかかったり、見間違えたりしてしまう恐れがあります。
そこで、リストには商品の名前、場所、数量など必要最低限の情報だけを載せて、作業員がすぐに理解できるようにしましょう。
働きやすい環境を作る
倉庫は夏は暑くて冬は寒く、かなり厳しい環境になるところが少なくありません。
このような環境下では疲労しやすく、作業員の集中力が下がり、作業ミスを招いてしまうかもしれません。
そこで、エアコンを設置したり、防寒着を用意したりと、働きやすい環境を作りましょう。
質問しやすい環境を用意する
ピッキングについて分からないことがある場合、そのままにして作業を進めると多くのミスが発生し、対処に追われてしまいます。
このような事態を防ぐためにはまだ慣れていない人には担当者をつけたり、「気軽に質問してください」と伝えたりと、分からない人が誰かに気軽に質問できるような環境を用意しましょう。
まとめ
ピッキングは入荷から出荷までの作業のうち、最も時間を使うものの1つです。
そのため、ピッキングを効率化すればより生産性を高めることができ、売上を上げることにも繋がります。
効率化するときにはレイアウトを作り直したり、ハンディを使ってピッキングできるようにしたりと色々な方法があります。
企業の規模や予算、さらに抱えている課題に合わせて最適な改善策を取り入れ、ピッキング作業の効率化を実現しましょう。