この記事では次の内容をまとめています。
- MES(製造実行システム)とは
- MESを利用するメリット
- MESを利用するデメリット
MESを利用しようか迷っている工場が知っておくべきことを全てまとめました。
工場の生産効率を上げるMES(製造実行システム)とは
MESとは”Manufacturing Execution System”の略で、「製造実行システム」という意味です。
各製造工程と連携し、次のようなことを行います。
- 工程の管理
- 作業者への指示
- 生産データの分析
- 品質管理
- 設備のメンテナナンス
工場にある人材、設備、時間といった資源を最適化して、生産効率の最大化を目指します。
かつて日本は大量に生産し、大量に売り捌く大量消費の時代でしたが、今は少量多品種の時代になっており、1つの工場で様々な種類の製品を生産するようになりました。
MESはそんな時代にとても合うシステムです。
MESの11の機能
MESには主に11の機能があり、必要に応じてそれぞれの機能が使われます。
この章では11の機能を簡単にご紹介します。
- 生産資源の配分と監視
- 仕様・文書管理
- 保守・保全管理
- 品質管理
- 作業のスケジューリング
- 差立・製造指示
- 作業者管理
- データ収集
- プロセス管理
- 製品の追跡と製品体系の管理
- 実績の分析
工場がMESを利用するメリット7つ
この章では工場がMESを利用するメリットをご紹介します。
1 | 生産効率を最大化できる |
2 | リードタイムを短縮できる |
3 | トラブルの原因を突き止めやすい |
4 | 品質が安定する |
5 | 施策の効果を測定できる |
6 | 部署間の情報共有がしやすい |
7 | 製造の属人化を防げる |
生産効率を最大化できる
MESを導入すると生産効率を最大化できます。
MESでは製造工程を監視しているため、非効率的な工程を見つけ、改善に繋げることができます。
また、設備や従業員の稼働状況をリアルタイムで把握することで適切な指示を出します。
製造の無駄をなくすことで工場の生産能力は高まり、業績アップも狙えます。
リードタイムを短縮できる
生産効率が上がることでリードタイムは短縮されます。
すると様々なメリットが生まれます。
例えば、製品が速く顧客の元に届くようになり、満足度が上がります。
また、競合他社との差別化の要素になり、企業の競争力を高めることができます。
さらには需要の変化に柔軟に対応できるため、在庫を最適化しやすくなるというメリットもあります。
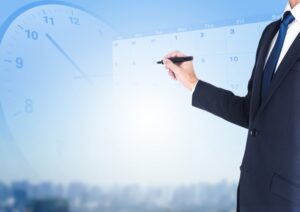
トラブルの原因を突き止めやすい
MESでは不良品の発生などのトラブルの原因を突き止めやすいです。
なぜかというと、製造工程を常に監視し、データも残っているため、追跡ができるからです。
そのため、もしも不良品が発生したとしても、不良品が紛れている可能性がある範囲を最小限に絞り込むことができ、回収やロスの数を抑えられます。
トラブルの対処にかかる時間も減らせて、あらゆる面で無駄を省くことができます。
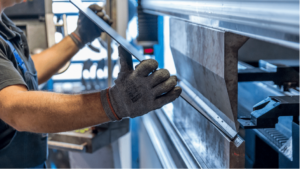
品質が安定する
トラブル時にすぐに原因を突き止め、改善策を実行することを繰り返すことによって製品の品質が安定します。
品質が安定すれば顧客の元に不良品が届くことも少なくなり、企業イメージを保つことができます。
また、トラブル対応に時間を割く必要がなくなり、本当に必要な業務に集中できることで業績アップに繋がります。
施策の効果を測定できる
MESは生産データを収集し、残します。
そのため、製造工程において何か施策を行った際の分析が容易になります。
施策をする際、実行するだけで、効果測定や振り返りをしないケースは少なくありません。
こうした施策は結果を分析してこそ、次に繋がります。
そこで、何か施策を実行に移したらMESを活用しながら効果を測定し、また次の施策を考えるサイクルを繰り返すことで、より精度が高く、生産効率も良い製造を目指しましょう。
部署間の情報共有がしやすい
会社にMESを導入すると、部署間の情報共有がしやすくなります。
これはMESで作業の進捗状況や生産計画をどの部署もリアルタイムで把握することができるからです。
もしも生産計画に急な変更が生じてもスムーズに伝達でき、作業者への指示もすぐにできるため、今までに比べて各部署間でのコミュニケーションにかかっていた時間を大幅に削減できます。
製造の属人化を防げる
MESでは技術やノウハウをデータとして蓄積することができます。
そのため、製造技術の属人化を防ぐことができます。
製造業では1人の職人に技術が属人化していることが珍しくありません。
この状況にはその職人が居なくなった場合に企業から技術が消えてしまうというリスクがあります。
製造業では職人の高齢化や人手不足が問題となっており、個々のノウハウを会社全体で共有する重要性が高まっています。
MESはこれを実現します。ノウハウをマニュアル化し、新人に教育できる仕組みを作っていれば、技術継承が容易になりますし、研修や教育にかける時間を削減できます。
工場がMESを利用するデメリット3つ
この章では工場がMESを導入する際に知っておくべきデメリットをご紹介します。
1 | 導入にコストがかかる |
2 | 目的が明確でないと効果が出にくい |
3 | 従業員が使いこなすまでに時間がかかる |
導入にコストがかかる
MESを導入する際にはコストがかかります。
また、使い続けることでランニングコストも発生します。
そのため、MESを使用することによって、初期投資やランニングコスト以上の見返りがあるかどうかを導入前に慎重に検討する必要があります。
目的が明確でないと効果が出にくい
MESはただ導入すれば良いわけではありません。
導入する目的を明確にし、それを実現できる機能を備えたシステムを選ぶことで効果が出ます。
工場には様々な課題があるはずです。
それを一度に解消することを目指すのではなく、課題の重要性において優先順位をつけて、計画的に解消することで効率的に環境が改善されていきます。
また、MESを導入する目的を現場の社員にも共有することで、解決するまでの期間は短くなるはずです。
このように導入前から目的意識を持っておけば、コスト以上の結果を得られます。
従業員が使いこなすまでに時間がかかる
現場でMESを使いこなすには専門知識が必要です。
そのため、工場にMESを導入する際は研修を行う必要があります。
従業員がシステムを使いこなせるようになるまで一時的に生産性が落ちてしまうこともあるかもしれません。しかし、慣れてくると、スムーズに使えるようになり、生産効率向上に大きく貢献します。
新しいシステムの導入に対して、最初は社員が戸惑うこともあるかもしれないので、システムを導入する意味や目的を伝えて理解してもらいましょう。
工場がMESを選ぶときに見るべきポイント4つ
この章では工場がどのシステムを導入するかを決めるときに見るべきポイントをご紹介します。
1 | 機能 |
2 | データ収集の方法 |
3 | 複数拠点に対応できるか |
4 | 自社の業種に合っているか |
機能
まず、機能はシステム選びの際に欠かせないポイントです。
MESは企業によって大まかなシステムの内容は同じでも、機能やできることが微妙に異なります。
自社に合った機能を持つMESを見つけるには、先ほどもご説明したように解決すべき課題とMESを導入する目的を明確にすることが欠かせません。
データ収集の方法
MESでは製造工程における大量のデータを収集し、蓄積します。
このデータをどのように集めるのかもシステム選びで注目すべきポイントです。
例えば、設備や機械から自動でデータを収集するものや、ハンディやRFIDで取り込むものなど、様々なやり方があります。
作業者の負担になりにくく、且つ、使いやすい方法を選ぶのが理想的です。
複数拠点に対応できるか
拠点をいくつか持つ企業の場合は複数拠点に対応できるMESを選びましょう。
それぞれの拠点で別々のMESを利用するよりも、一元管理できるものを選んだ方が、各地の進捗が一目で分かり、とても便利です。
中には海外の拠点にも対応できるものもあります。
自社の業種に合っているか
自社の業種を得意とするMESを選ぶことも大切です。
同じ工場用のMESでも、アパレル、食品、化学品など、それぞれ得意分野を持っているケースがあります。
自社に合うものを選べばより結果が出やすくなるでしょう。
各MESの導入実績を調べたり、担当者から話を聞いたりして、最適なシステムを選びましょう。
まとめ
MESは製造実行システムとも呼ばれ、製造工程の管理や作業員への指示を行い、会社の人材、設備、時間を最大限に生かす製造を実現します。
ただし、MESを導入するだけで効果が出るわけではなく、工場の課題に合うものを選ぶことで効果が出やすくなります。
MESを導入する目的を明確にしてからシステムを選びましょう。